Article
Cover
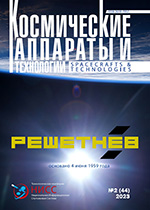
Title
Prospects for the application of various methods of vibration processing in the welded structures of spacecraftAuthors
K.E. Ponomarev, I.V. StrelnikovOrganization
JSC «NPO Lavochkina»Khimki, Moscow region, Russian Federation
Abstract
The possibility of using vibration technologies as an alternative to heat treatment, but having a shorter duration, low energy consumption, low capital costs and comparable efficiency, is substantiated. Priority areas of application of methods of vibration treatment of critical welded structures are highlighted: post-welding and related. The advantages and difficulties in the implementation of these methods are shown: the ability to control the efficiency of postwelding processing by changing the amplitude-frequency characteristics, increasing strength and plasticity and optimizing the geometric parameters of the weld, combining the processing time together with the welding production cycle with accompanying processing. Brief results of experimental work on the criteria of residual stresses and residual deformations for different types of welded joints, such as butt, T-bar and lap joints, and several groups of materials, such as aluminum alloys, carbon steels and stainless steels, are presented. The conclusion is made about the prospects of using post-welding vibration treatment for dimensional rigid, forming a closed contour, composed of their many parts and subassemblies of welded structures in assembly-welding special conductors or universal assembly devices, as well as about the initial reduction of residual deformations during concomitant vibration treatment of welded joints.Keywords
vibration treatment, arc welding, concomitant vibration treatment, post-welding vibration treatment, residual deformation, residual stressReferences
[1] Sagalevich V. M. Ustranenie svarochnyh deformacij v mashinostroitel'nyh konstrukciyah [Elimination of welding deformations in machine-building structures]. Moscow, Niinformtyazhmash, 1969, 79 p. (In Russian)
[2] Dryga A. I. Vibrostabiliziruyushchaya obrabotka svarnyh i lityh detalej v mashinostroenii (teoriya, issledovaniya, tekhnologiya) [Vibration-stabilizing treatment of welded and cast parts in mechanical engineering (theory, research, technology)]. Kramatorsk, DGMA, 2004, 168 p. (In Russian)
[3] Govindarao P., Gopalakrishna A. Affect of vibratory welding process to improve the mechanical properties of butt welded joints // International journal of modern engineering research, 2012, vol. 2, issue 4, pp. 2766–2770.
[4] Shaikh S. N. Vibratory Residual Stress Relieving- A Review // Journal of Mechanical & Civil Engineering, 2016, no. 3, pp. 01–04. doi: 10.9790/1684-15008030301-04.
[5] Jose M. J., Kumar S. S., Sharma A. Vibration assisted welding processes and their influence on quality of welds // Science and Technology of Welding & Joining, 2016, issue 4, pp. 45–49. doi: 10.1179/1362171815Y.0000000088.
[6] Laschenko G. I. Tekhnologicheskie vozmozhnosti vibracionnoj obrabotki: obzor [Technological possibilities of vibration processing: review] // Automatic welding, 2016, no. 7, pp. 28–34. (In Russian)
[7] Ebrahimi S. M., Farahani M., Akbari D. The influences of the cyclic force magnitude and frequency on the effectiveness of the vibratory stress relief process on a butt welded connection // The International Journal ofAdvanced Manufacturing Technology, 2019, vol. 102, pp. 2147–2158. doi: 10.1007/s00170-019-03288-y.
[8] Singh J., Kumar G., Garg N. Influence of vibrations in arc welding over mechanical properties and microstructure of butt-welded-joints // International Journal of Science & Technology, 2012, vol. 2, issue 1, pp. 1–6.
[9] Ponomarev K. E., Strelnikov I. V. K voprosu primeneniya vibracionnoj obrabotki svarnyh konstrukcij kosmicheskih apparatov dlya povysheniya tochnosti i razmernoj stabil'nosti. Obzor [On the application of vibration processing of welded spacecraft structures to improve accuracy and dimensional stability. Review] // Vestnik NPO im. S. A. Lavochkina, 2017, no. 4 (38), pp. 89–95. (In Russian)
[10] Strelnikov I. V. Vliyanie soputstvuyushchej vibracionnoj obrabotki na ostatochnuyu deformaciyu i geometriyu svarnyh soedinenij peremennoj zhestkosti [Influence of concomitant vibration treatment on residual deformation and geometry of welded joints of variable stiffness] // Welding and Diagnostics, 2018, no. 3, pp. 24–29. (In Russian)
[11] Ponomarev K. E., Strelnikov I. V., Antonov A. A., Utkin I. Yu. Ocenka vliyaniya parametrov rezhima soputstvuyushchej vibracionnoj obrabotki na ostatochnye napryazheniya alyuminievyh svarnyh konstrukcij s privlecheniem polnogo faktornogo eksperimenta [Evaluation of the influence of the parameters of the mode of concomitant vibration treatment on the residual stresses of aluminum welded structures with the involvement of a full factor experiment] // Welding and diagnostics, 2022, no. 2, pp. 30–33. (In Russian)
[12] Ratnathicam Sh. A study of the effect of vibration on the residual stresses in a welded fabricated tube // Thesis of Master of Science in Applied Science, Portland State University, 1979, 84 р. doi: 10.15760/etd.2891.
[13] Sedec P. Vibrationtreatment–effective method of improving the dimensional stability of welded structures: investigation and practice // Welding and Surfacing, 1997, vol. 8, pp. 221–228.
[14] Aoki S. Reduction of Residual Stress by Ultrasonic Surface Vibration // Japanese Society of Mechanical Engineers, 1995, pp. 173–177.
[15] Ponomarev K. E., Strelnikov I. V. K voprosu vybora eksperimental'nogo metoda ocenki ostatochnyh napryazhenij v svarnyh konstrukciyah [On the issue of choosing an experimental method for assessing residual stresses in welded structures] // Welding and Diagnostics, 2018, no. 2, pp. 29–34. (In Russian)
For citing this article
Ponomarev K.E., Strelnikov I.V. Prospects for the application of various methods of vibration processing in the welded structures of spacecraft // Spacecrafts & Technologies, 2023, vol. 7, no. 2, pp. 126-131. doi: 10.26732/j.st.2023.2.05
This Article is licensed under a Creative Commons Attribution-NonCommercial 4.0 International License (CC BY-NC 4.0).